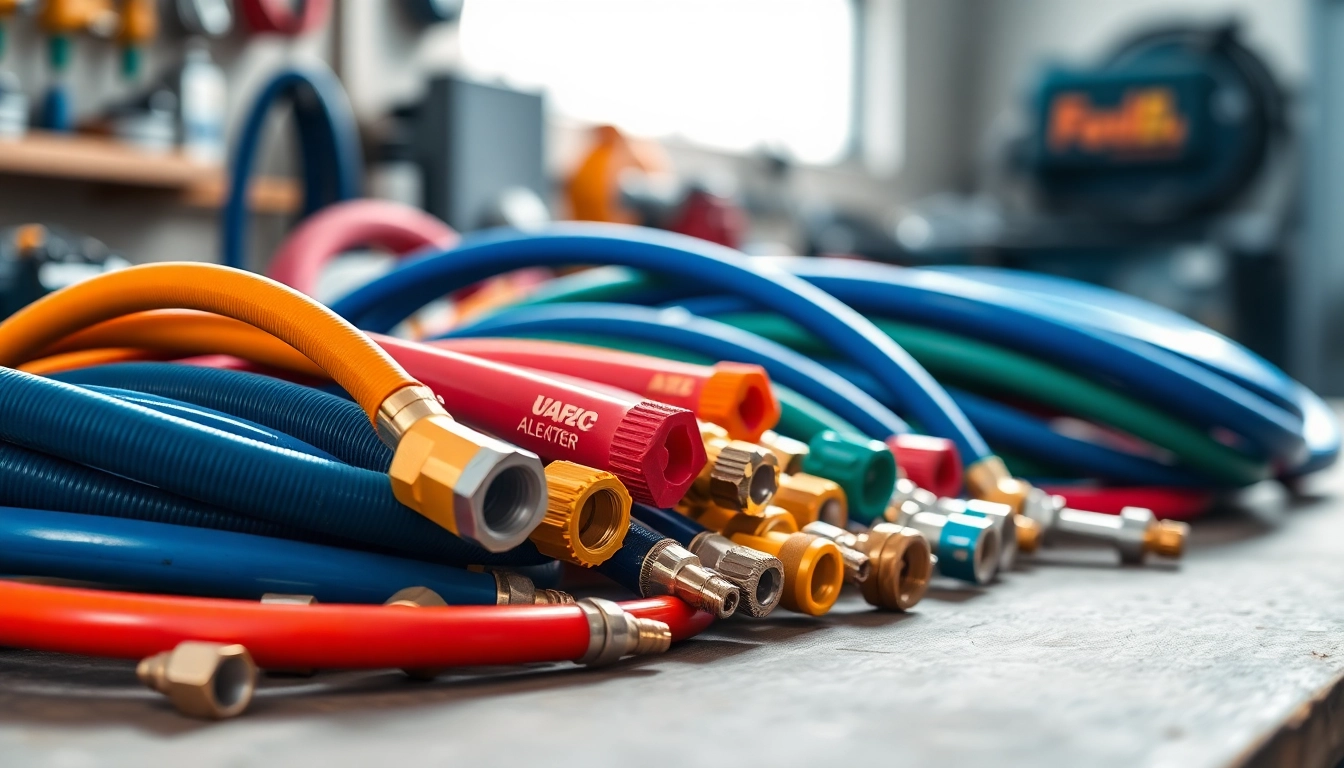
Understanding Air Hoses and Fittings
What are Air Hoses and Fittings?
Air hoses and fittings are essential components utilized in a variety of applications involving compressed air systems. Air hoses are flexible tubes designed to transport compressed air from a compressor to pneumatic tools, accessories, or other equipment. They are typically made from materials such as rubber, PVC, or polyurethane, each offering unique properties suitable for different environments and usages. Fittings, on the other hand, are the connectors that join different sections of hose or attach hoses and tools to air compressors. Air hoses and fittings play a critical role in maintaining the efficiency and safety of pneumatic systems.
Importance of Quality in Air Compressors
The quality of air hoses and fittings directly impacts the performance and longevity of air compressors and pneumatic tools. Inferior products can lead to leaks, reduced airflow, and even equipment failure, which can be both dangerous and costly. For this reason, investing in high-quality hoses and fittings is paramount. These components should be durable enough to withstand the pressures of operation and the environment in which they are used—whether that’s extreme temperatures, exposure to chemicals, or constant wear and tear from use.
Common Types of Air Hoses and Their Uses
There are several types of air hoses, each designed for specific applications:
- Rubber Hoses: Known for their flexibility and durability, rubber hoses are excellent for high-pressure environments and extreme conditions.
- PVC Hoses: These hoses are lightweight, affordable, and less prone to kinking, making them suitable for light-duty applications.
- Polyurethane Hoses: Offering a good balance of weight and flexibility, polyurethane hoses are ideal for use in colder climates.
- Hybrid Hoses: Combining the advantages of rubber and PVC, hybrid hoses are flexible in cold weather and resistant to abrasion.
How to Choose the Right Air Hose
Factors to Consider When Selecting Air Hoses
Choosing the right air hose involves several considerations:
- Diameter: The hose diameter should match the tool requirements and air-pressure output of the compressor to ensure efficient airflow.
- Length: Measure the distance between your compressor and tools to select an appropriate length, avoiding excess slack that can lead to tangling or kinking.
- Material: Consider where the hose will be used; materials affect flexibility, weight, and durability.
- Pressure Rating: Ensure the hose can handle the maximum pressure produced by your compressor.
Matching Fittings with Your Air Hose
Fitting selection is as crucial as choosing the hose. The fittings must be compatible in size and type with both tools and hoses. Common fittings include couplers, plugs, and adapters, which may vary in thread type and size. Always check for specifications to identify compatible fittings for your equipment.
Understanding Pressure Ratings and Lengths
Pressure ratings indicate the maximum safe pressure a hose can handle, while lengths affect the efficiency of air delivery. Selecting a hose that meets or exceeds your compressor’s output pressure is essential for safe operation. Lengthwise, longer hoses can lead to pressure drops that minimize tool performance, requiring a careful balance between accessibility and efficiency.
Best Air Hose Materials
Rubber vs. Hybrid Hoses
Rubber hoses are well-regarded for their superior flexibility and durability, particularly in rugged conditions. However, they can be heavier and less convenient to handle over long distances. Hybrid hoses, on the other hand, are designed to provide the best of both worlds: they combine the strength and durability of rubber with the lightweight characteristic of PVC. This versatility makes hybrid hoses an attractive choice for various tasks, from daily DIY projects to industrial applications.
Advantages of PVC and Polyurethane
PVC hoses are an economical choice, providing resistance to kinks and abrasions, making them ideal for environments with less rigorous demands. Polyurethane hoses, although slightly more costly, feature excellent flexibility and are lighter, which may be a crucial factor in mobility-intensive jobs. They also handle extreme temperatures better than PVC and rubber options.
Durability and Flexibility in Hoses
The long-term effectiveness of air hoses depends significantly on their durability and flexibility. Rubber hoses excel in harsh environments; however, they can become brittle over time if not properly maintained. Polyurethane and hybrid hoses provide excellent performance in various temperatures, maintaining flexibility without sacrificing durability.
Connecting Air Hoses Safely
Types of Fittings and Their Applications
Fittings are designed for specific applications, and understanding their types can enhance your system’s functionality:
- Quick Connect Couplers: These allow for fast and convenient connection and disconnection of hoses.
- Threaded Fittings: Commonly used in permanent installations, these provide a secure connection but require wrenches for installation and removal.
- Barbed Fittings: Used primarily with flexible hoses, barbed fittings create a tight connection, often secured with clamps.
Installation Tips for Air Hoses and Fittings
Proper installation of air hoses and fittings is critical for optimal performance. Here are some essential tips:
- Inspect all components before installation for any damages or wear.
- Use thread sealants on threaded connections to prevent air leaks.
- Ensure hoses and fittings match in size and pressure rating.
- Avoid excessive bending or tangling of the hose during installation.
Common Mistakes to Avoid When Connecting
To ensure longevity and efficiency, be mindful of common pitfalls:
- Using incompatible fittings that may cause leaks or breaks.
- Failing to check the hose for kinks or twists that restrict airflow.
- Neglecting to properly tighten fittings, which can lead to air loss.
- Overstretching hoses, particularly when operating in tight spaces.
Caring for Air Hoses and Fittings
Maintenance Tips for Extended Life
Regular maintenance prolongs the life of air hoses and fittings. Here are effective practices:
- Store hoses properly on reels or in coiled positions to prevent kinks.
- Inspect hoses and fittings regularly for signs of wear, cracks, or leaks.
- Clean hoses by blowing air through them to remove debris.
- Keep fittings lubricated to allow easy connection and disconnection.
Signs of Wear and Replacement Guidelines
It’s essential to recognize when it’s time to replace hoses and fittings to maintain safety and functionality. Look for:
- Cracks or cuts in the hose material.
- Decreased flexibility or stiffness in the hose.
- Visible signs of leaks at fittings or along the hose.
- Changes in the performance of tools connected to the hose.
Storing Your Air Hoses Properly
Proper storage is vital to maintain the integrity of your air hoses and fittings. Store them in a cool, dry environment and avoid direct exposure to sunlight or extreme temperatures. Using storage reels or hooks can prevent tangling and kinking, ensuring that tools are always ready for immediate use.