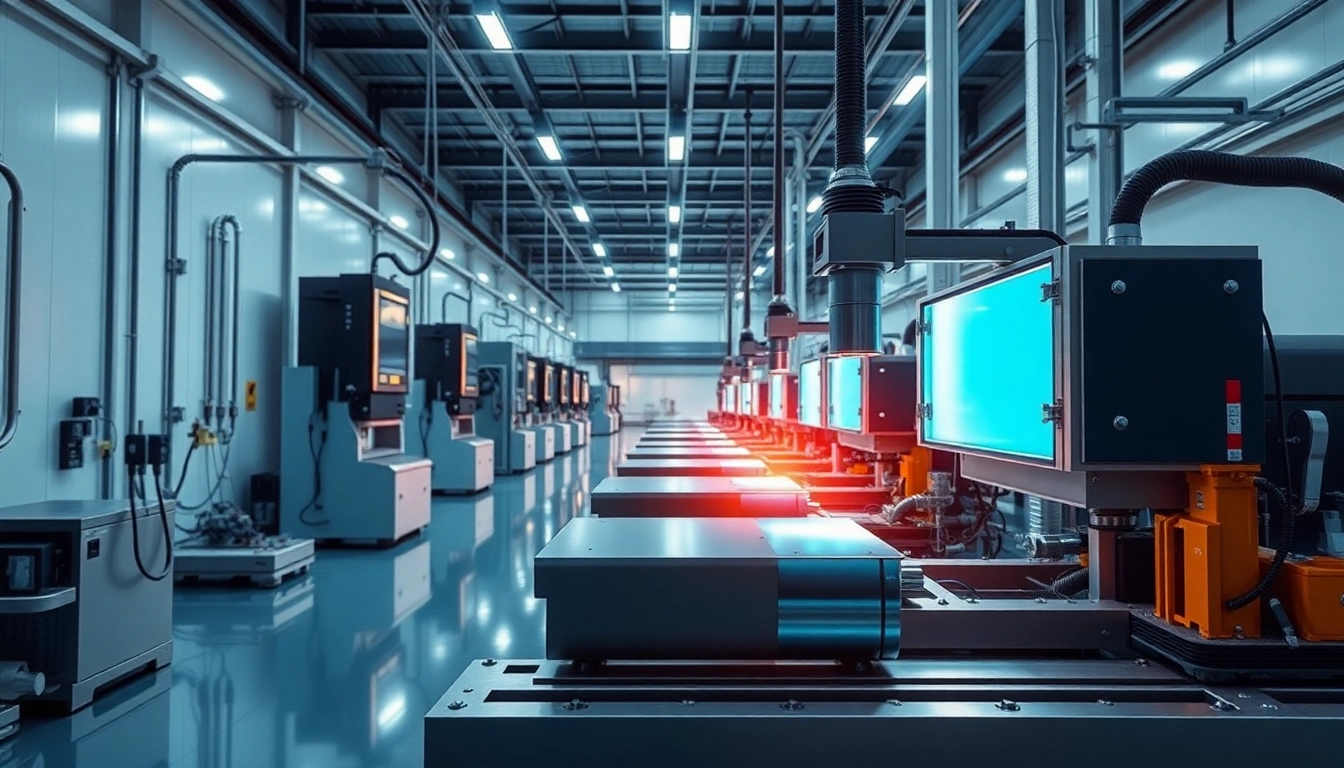
What is EP Coating?
Defining Electrophoretic Coating
Electrophoretic coating, often abbreviated as EP coating, is a revolutionary surface finishing technique utilized primarily for conductive materials. The process employs an electric current to facilitate the deposition of paint on metal surfaces, which enhances their resistance to corrosion and improves overall durability. In essence, the painting process involves immersing the items to be coated in a specially formulated paint bath, followed by the application of an electrical charge that attracts paint particles to the substrate. This method, also known as e-coating or electrocoating, has been embraced across various industries, including automotive, electronics, and appliances, making it an essential coat technology in contemporary manufacturing.
How EP Coating Works
The operation of electrophoretic coating is founded on the principles of electrolysis. Initially, the substrate is prepared by cleaning and often pre-treating to rid it of any contaminants. Once prepared, the item is submerged in an aqueous paint solution containing charged pigment particles. When an electrical current is applied, the oppositely charged particles migrate toward the substrate, forming a uniform film as they deposit on the surface. The thickness of this film can typically range from 15 to 30 microns, depending on the specific requirements of the application.
After deposition, the coated item is removed from the bath and subsequently cured in an oven at elevated temperatures, enabling the paint to bond effectively with the metal surface, creating a durable and resistant finish. This curing process also solidifies the coating, enhancing its adhesion properties and overall performance under various environmental conditions.
Types of EP Coating Materials
The materials used in the electrophoretic coating process can vary significantly. Depending on the desired properties of the finish, manufacturers often opt for specific formulations. Common materials include:
- Epoxy-based coatings: They provide superior corrosion resistance and are typically used in environments prone to high humidity.
- Polyester-based coatings: Known for their excellent UV resistance, these coatings are ideal for outdoor applications.
- Hybrid coatings: Combining the best characteristics of both epoxy and polyester, hybrid coatings offer versatility across multiple applications.
Benefits of Using EP Coating
Enhanced Corrosion Resistance
One of the most compelling reasons for the adoption of electrophoretic coating is its exceptional resistance to corrosion. Because EP coatings create a continuous barrier over the substrate, they significantly reduce the penetration of moisture and corrosive elements. This makes them particularly valuable in automotive and marine applications, where components are frequently exposed to extreme environmental conditions. Reports indicate that EP-coated parts can endure salt spray tests, surpassing 1,000 hours of exposure without exhibiting substantial corrosion, making them a reliable choice for manufacturers concerned about longevity.
Uniform Coating Distribution
The electrophoretic coating process is particularly notable for its ability to provide uniform coverage, even in complex geometries and hard-to-reach areas. The electrical nature of the process ensures that the paint is deposited evenly, which is crucial in maintaining the aesthetic and functional properties of coated items. As a result, EP coatings are less likely to have defects, such as runs, sags, or uneven thicknesses compared to traditional painting methods.
Cost-Effectiveness in Manufacturing
In addition to its performance benefits, EP coating is often more cost-effective compared to alternative finishing methods. The process allows for high production speeds, leading to quicker turnaround times. Moreover, the efficient use of materials minimizes waste, further trimming down costs associated with raw materials. Industries are increasingly recognizing that while the initial investment in EP coating equipment may be higher, the long-term savings on material, labor, and increased durability make it a sound investment.
EP Coating in Various Industries
Automotive Applications
In the automotive sector, ep coating is extensively used to protect various components such as chassis parts, suspension systems, and body panels. The ability to provide a robust protective barrier against rust and wear translates to improved vehicle longevity and performance. For instance, leading automotive manufacturers implement EP coatings to enhance the lifespan of metal parts exposed to fluctuating weather conditions and road debris, significantly reducing maintenance costs over time.
Electronics and Electrical Components
The electronics industry also benefits extensively from EP coating technologies. Electronic components require protection from environmental factors such as moisture, dust, and chemicals that could compromise their functionality. EP coatings offer a thin, lightweight finish that does not interfere with component performance while providing necessary environmental protection. Additionally, these coatings facilitate electromagnetic interference (EMI) shielding, promoting the reliability and durability of electronics.
Aerospace Industry Benefits
In aerospace applications, the weight and performance of components are critical factors. EP coatings provide an ideal solution as they add minimal weight while offering exceptional protection against severe environmental exposure, including temperature extremes and corrosion. For example, aerospace manufacturers utilize EP coatings on parts like engine casings and landing gear to ensure longevity and safety, critical in aviation applications.
EP Coating Process and Techniques
Steps Involved in EP Coating
The EP coating process can be broken down into several critical steps, each contributing to the overall effectiveness of the coating:
- Surface Preparation: The items need to be thoroughly cleaned and pre-treated to remove contaminants that could inhibit coating adhesion.
- Coating Bath: Prepared components are submerged in a paint bath where they receive an electrical charge.
- Electrodeposition: As the electric current is applied, paint particles migrate and adhere to the substrate, forming a uniform coat.
- Rinsing: Once coated, parts are rinsed to remove any unbound paint.
- Curing: The final coating is accomplished by curing in an oven, where heat helps solidify the paint and ensure strong adhesion.
Common Challenges and Solutions
While the benefits of EP coating are substantial, challenges can arise during the process, including:
- Inconsistent Coating Thickness: Achieving uniform thickness on parts with complex shapes can be problematic. This challenge can be mitigated by optimizing the coating bath parameters, such as pH and electrical settings.
- Adhesion Issues: Poor surface preparation may lead to adhesion failures. Implementing a rigorous cleaning and pre-treatment regimen can resolve most adhesion issues.
- Environmental Constraints: EP coating facilities must manage environmental parameters. Regular monitoring of the coating environment, including temperature and humidity, can ensure a quality finish.
Performance Metrics for Coating Quality
To evaluate the success of the EP coating process, several performance metrics are commonly assessed, including:
- Thickness Measurement: Ensuring the applied coating meets specified thickness standards is paramount to performance.
- Adhesion Testing: Testing for adhesion strength often entails cross-hatch adhesion tests to verify the durability of the bond.
- Corrosion Resistance Testing: Salt spray tests are frequently used to assess the ability of the coating to withstand corrosive environments.
Future of EP Coating Technology
Innovations in Coating Materials
The future of EP coating technology is bright, with continuous advancements in coating materials. Researchers are exploring innovative resins that enhance the environmental performance of coatings while maintaining functionality. Moreover, the development of specialized formulations that can withstand higher temperatures or chemicals holds promise for industries requiring extreme durability, such as aerospace and molecular electronics.
Environmental Impact and Sustainability
As industries worldwide pivot towards sustainability, EP coating technologies are undergoing transformations to minimize environmental impacts. Manufacturers are exploring eco-friendly materials and processes that reduce waste and solvent emissions. This shift not only complies with stringent regulations but also meets the growing consumer demand for sustainable products, positioning EP coatings as a forward-thinking solution in modern manufacturing.
Trends Shaping the EP Coating Industry
Several trends are shaping the landscape of EP coating, including:
- Automation: As manufacturing processes become increasingly automated, EP coating processes are being integrated into comprehensive production lines, reducing labor costs and improving consistency.
- Integration with Smart Technologies: The introduction of IoT technologies enables real-time monitoring and adjustments during the coating process, resulting in enhancements in quality control.
- Customization: With advancements in technology, custom formulations tailored to specific industry needs are becoming more accessible, enhancing the versatility of EP coating across applications.